Quality Science Pathway Apprenticeship – Employers & Collaborators
NEED: Recent biotechnology and biopharmaceutical workforce analyses for Greater Philadelphia identified access to a skilled workforce as one of the two largest barriers to industry growth and Quality Science among four crucially important job clusters necessary to sustain growth.
SOLUTION: To enable Greater Philadelphia’s life science industry to meet its growing workforce needs, The Wistar Institute is creating the Quality Science Pathway Apprenticeship (QSPA), a free program supported by the U.S. Economic Development Administration that will:
- Establish a state-registered apprenticeship in Quality Science
- Provide certification from Pathway for Patient Health as a Certified Quality Science Professional through an industry-developed curriculum taught by subject matter experts from regional employers
- Leverage federal Workforce Innovation and Opportunity Act funding to provide salary support for employers to offer on-the-job training
- Prepare apprentices for jobs in the biopharmaceutical industry, including Biomanufacturing, R&D, Regulatory Affairs, and Quality Assurance
During the fall and spring semesters, participants complete three industry-developed courses taught by subject matter experts from Philadelphia’s life science companies.
- Global Regulatory Requirements of Quality
- Product Development and Validation
- Risk Failure Analysis
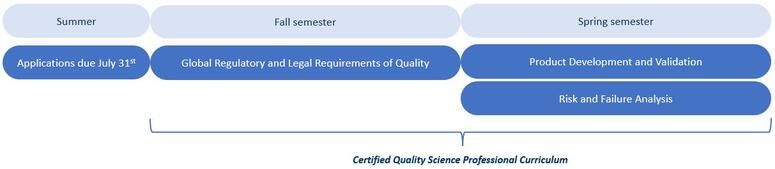
See enlarged view of timeline.
*Depending on prior coursework, students may also need to complete coursework in business and laboratory science
Throughout the program, apprentices will have an opportunity to be matched with employer partners for full-time employment and 2,000 hours of on-the-job training. Employers are eligible to receive reimbursement, typically at 50% of the apprentices’ salary for the first six months.
EMPLOYER VALUE
- Access a reliable talent pipeline for positions in Biomanufacturing, R&D, Regulatory Affairs, and Quality Assurance
- De-risk the hiring process
- Reduce onboarding time and effort
- Increase productivity and retention of new hires
DETAILED CURRICULUM
The Quality Science Pathway Apprenticeship (QSPA) curriculum is aligned with industry jobs including:
- Regulatory Affairs (Biopharmaceutical & Medical Devices)
- R&D (Biopharmaceutical & Medical Devices)
- Q&C Analyst
- Investigations
- Manufacturing Supervisor
- Validation Engineer
- Commercial Quality (Biopharmaceutical & Medical Devices)
- Risk Management
- GMP & GDP
Courses
(No Pre-requisite). 3 credit hour Pathway-Developed Course. Regulations serve as a foundation for good business decisions that protect and promote patient health. Faculty demonstrate the relationship between regulatory requirements, legal accountability and business responsibility, while introducing fundamental concepts in the regulations related to clinical trial development, management, ethics, data integrity, change control and validation. Topics such as the role of guidance documents and industry standards are reviewed, and case studies utilized to support the program. Understanding the “why” of the regulations fosters critical thinking grounded in science, data, stakeholder awareness and regulatory intelligence.
Learning Objectives
By the end of the Global Regulatory and Legal Requirements of Quality course, students will be able to:
- Understand why the industry is governed by Good Manufacturing Practices regulations, and how those regulations drive patient and business success.
- Identify risks associated with medical device, drug and human factors risks in order to, for example: (a) design process controls to reduce risk to product quality, (b) determine the correct classification of medical devices in order to design an appropriate development strategy, (c) identify primary and secondary clinical trial targets to demonstrate product safety and efficacy, and (d) understand risk to product on the market related to manufacturing failures.
- Describe the medical device and pharmaceutical Quality Systems, and how those systems enable organizations to consistently produce products that are of the purported quality and safety, and meet user needs.
- Recognize the significance of the data and studies needed to support product-related decisions made across the total product lifecycle.
(Prerequisite: The Global Regulatory and Legal Requirements of Quality course). 3 credit hour Pathway-Developed Course. Major design processes that are critical to life science product, process and specification development are explored in this course. Topics covered include: product and process development, design of experiments, variability, control, and validation methodology. Participants learn how rigorous human factor engineering studies and clinical trials provide essential inputs into the product development process. The participants are introduced to concepts such as gap analysis, risk assessment, process characterization, equipment qualification, measurement system analysis, repeatability and reproducibility, and performance qualification/ validation.
Learning Objectives
By the end of the Product Development and Validation course, students will be able to:
- Describe what needs to be studied and demonstrated during medical device and drug product development, from process controls, safety, efficacy, function, stability, scale-up, process validation and test method validation.
- Effective ways to monitor and predict product and process performance.
- Increasing right-first-time rates through enterprise-wide feedback loops to inform future product development.
(Prerequisite: The Global Regulatory and Legal Requirements of Quality course). 2 credit hour Pathway-Developed Course. Risk and failure analysis underpins every decision made in the life science industries. In this course, participants will be exposed to the use of risk analysis proactively to inform product development, as well as reactively to find true root cause to product, process, and system failures. Through the use of historical risk analysis techniques, such as FMEA, Fishbone, and 5 Why’s, participants are able to analyze a holistic set of data (in-production, across product lines, across equipment, human variability, on-market, on-stability, validation studies, change control, etc.) that lead to scientifically justified investigations supported by evidence, and the identification of effective corrective and preventative actions (CAPA).
Learning Objectives
By the end of the Risk and Failure course, students will be able to:
- Demonstrate practical use of risk management tools, such as 5 why’s, fishbone diagram, failure mode effect analysis and surveys.
- Assess a failure situation for root cause, impact to product (in production and on-market), trends, and corrective/preventative actions that will be effective at preventing recurrence.
- Demonstrate the experience gained in class with writing failure investigations that are supported by data and are scientifically sound.